A measure of the market risk of engineering plastics
Results for the 22 engineering plastics monitored by PricePedia
Published by Luigi Bidoia. .
technopolymers Procurement Risk ManagementIn the article The complexity in material selection: both technical criteria and market risk, Claudio Bruggi illustrated a case where, in selecting the engineering plastic for an injection-molded product, having a measure of the market risk of various technically suitable engineering plastics could be useful.
The complexity of this measure lies in the need to produce it not only for a single material but for multiple engineering plastics to allow for a comparison between them. In recent months, PricePedia has initiated a project specifically aimed at measuring, according to a standard methodology[1], the market risk of various commodities, making these measures comparable with each other. This article presents the results regarding a list of 22 engineering plastics.
The engineering plastics considered
Engineering plastics are advanced polymers that offer high performance, both mechanical and chemical, and are often used in technical and industrial applications where specific resistance properties are required. They can be grouped as follows:
- High-performance polymers: materials with high mechanical, thermal, or chemical properties, used in technical and industrial applications. Examples include Polyphenylene Sulfide (PPS), Epoxy resins, Liquid Crystal Polymers (LCP), and Poly(ethylene naphthalate-2,6-dicarboxylate) (PEN).
- Engineering polymers: materials with good structural properties, used in both technical applications and consumer goods. Key examples include Polycarbonates, Polyamides, Acetal resin (POM), and ABS copolymers.
- Advanced styrenic polymers: styrene-based materials with improved properties for more technical applications. Key examples include SAN copolymers.
- Fluorinated polymers: materials with excellent chemical and thermal resistance, often used in industrial and chemical applications. Examples include Polytetrafluoroethylene (PTFE), Tetrafluoroethylene copolymers, and Fluoroelastomer (FKM).
- Acrylic polymers: polymers derived from acrylic acid, used for transparency, UV resistance, and aesthetic properties. Key examples include Polymethyl Methacrylate (PMMA), Thickening acrylic polymers, and Methyl acrylate copolymers.
- Other special and innovative polymers: including Vinylidene chloride copolymers (PVDC), Advanced maleic anhydride-based polymers, and Poly(1,3-phenylene methylphosphonate).
Global supply of engineering plastics
The following two tables compare exports for major engineering polymers by major exporting countries in the years 2010 and 2023.
Main engineering plastics exporters in 2010 (millions of dollars)
Engineering plastics | United States | Germany | Belgium | Holland | China | Korea | Japan |
ABS copolymers | 244 | 261 | 499 | 146 | 119 | 2779 | 403 |
Acetal resin (POM) | 239 | 0 | 250 | 25 | 105 | 167 | 176 |
Advanced maleic anhydride-based polymers | 215 | 226 | 74 | 52 | 28 | 14 | 102 |
Epoxy resins | 877 | 931 | 98 | 445 | 237 | 508 | 582 |
Fluoroelastomer FKM | 106 | 62 | 29 | 89 | 25 | 4 | 125 |
Liquid Crystal Polymers (LCP) | 21 | 25 | 9 | 13 | 8 | 16 | 19 |
Methyl acrylate copolymers | 84 | 2 | 4 | 57 | 1 | 1 | 2 |
Other Polyamides (4.6, 4.10, 6.3-T, 6.36, 12.12) | 442 | 494 | 195 | 209 | 163 | 28 | 206 |
Other advanced polymers (PEI, PDCPD, and others) | 334 | 658 | 61 | 68 | 49 | 30 | 187 |
Other advanced styrenic polymers | 435 | 391 | 599 | 292 | 34 | 553 | 338 |
Poly(1,3-phenylene methylphosphonate) | 0 | 0 | 0 | 0 | 0 | 0 | 0 |
Poly(ethylene naphthalate-2,6-dicarboxylate) (PEN) | 9 | 18 | 7 | 10 | 4 | 31 | 28 |
Polyamide (PA) | 1769 | 1952 | 1161 | 657 | 296 | 445 | 413 |
Polycarbonates (PC) | 1164 | 10 | 0 | 616 | 877 | 1012 | 638 |
Polymethyl methacrylate (PMMA) | 76 | 0 | 14 | 9 | 43 | 278 | 241 |
Polyphenylene sulfide (PPS) | 120 | 23 | 66 | 7 | 11 | 3 | 56 |
Polytetrafluoroethylene (PTFE) | 127 | 116 | 32 | 119 | 168 | 3 | 54 |
SAN copolymers | 86 | 0 | 21 | 26 | 18 | 206 | 112 |
Saturated polyesters | 622 | 961 | 376 | 492 | 274 | 517 | 630 |
Tetrafluoroethylene copolymers | 158 | 77 | 35 | 108 | 35 | 6 | 186 |
Thickening acrylic polymer | 10 | 1 | 4 | 5 | 1 | 1 | 2 |
Vinylidene chloride polymers (PVDC) | 50 | 1 | 4 | 7 | 0 | 0 | 67 |
Main engineering plastics exporters in 2023 (millions of dollars)
Engineering plastics | United States | Germany | Belgium | Holland | China | Korea | Japan |
ABS copolymers | 284 | 127 | 514 | 331 | 260 | 1802 | 127 |
Acetal resin (POM) | 361 | 408 | 338 | 303 | 84 | 363 | 134 |
Advanced maleic anhydride-based polymers | 267 | 279 | 120 | 104 | 188 | 83 | 212 |
Epoxy resins | 817 | 1003 | 68 | 343 | 411 | 868 | 458 |
Fluoroelastomer FKM | 218 | 107 | 22 | 162 | 270 | 12 | 216 |
Liquid Crystal Polymers (LCP) | 31 | 8 | 7 | 22 | 24 | 1 | 9 |
Methyl acrylate copolymers | 149 | 6 | 94 | 1 | 44 | 4 | 3 |
Other Polyamides (4.6, 4.10, 6.3-T, 6.36, 12.12) | 686 | 754 | 340 | 253 | 329 | 112 | 211 |
Other advanced polymers (PEI, PDCPD, and others) | 330 | 669 | 145 | 91 | 298 | 127 | 248 |
Other advanced styrenic polymers | 587 | 361 | 550 | 221 | 107 | 668 | 256 |
Poly(1,3-phenylene methylphosphonate) | 2 | 0 | 1 | 0 | 0 | 0 | 0 |
Poly(ethylene naphthalate-2,6-dicarboxylate) (PEN) | 7 | 17 | 4 | 5 | 14 | 5 | 5 |
Polyamide (PA) | 1998 | 1840 | 927 | 466 | 1428 | 301 | 257 |
Polycarbonates (PC) | 1054 | 0 | 0 | 649 | 881 | 1525 | 513 |
Polymethyl methacrylate (PMMA) | 123 | 0 | 42 | 41 | 74 | 248 | 106 |
Polyphenylene sulfide (PPS) | 170 | 41 | 60 | 57 | 58 | 49 | 88 |
Polytetrafluoroethylene (PTFE) | 114 | 180 | 53 | 121 | 251 | 9 | 92 |
SAN copolymers | 49 | 0 | 9 | 40 | 58 | 227 | 40 |
Saturated polyesters | 1066 | 1421 | 558 | 510 | 1144 | 417 | 486 |
Tetrafluoroethylene copolymers | 373 | 127 | 80 | 69 | 297 | 17 | 356 |
Thickening acrylic polymer | 6 | 2 | 2 | 7 | 3 | 2 | 1 |
Vinylidene chloride polymers (PVDC) | 4 | 2 | 99 | 6 | 23 | 1 | 37 |
The comparison between the two tables clearly highlights the following points:
- In the last 13 years, the value of Chinese exports of engineering plastics has increased by $3.7 billion, while U.S. and German exports have grown by $1.5 billion and $1.1 billion, respectively. After becoming the world’s largest producer, China is now set to become the leading exporter in the coming years;
- With over $800 million, China is already the world’s top exporter of fluorinated engineering plastics (Polytetrafluoroethylene (PTFE), Tetrafluoroethylene copolymers, and Fluoroelastomer (FKM));
- Chinese exports of polyamides and saturated polyesters have shown particularly high growth, placing China among the top exporters globally, alongside the United States and Germany;
- South Korea has reached the top position in polycarbonate exports and continues to hold an undisputed leadership position in ABS copolymers, although its exports have declined in recent years.
A measure of market risk
Using the methodology developed by PricePedia[1], we have measured the market risk of the 22 engineering plastics considered.
The following chart shows the results obtained.
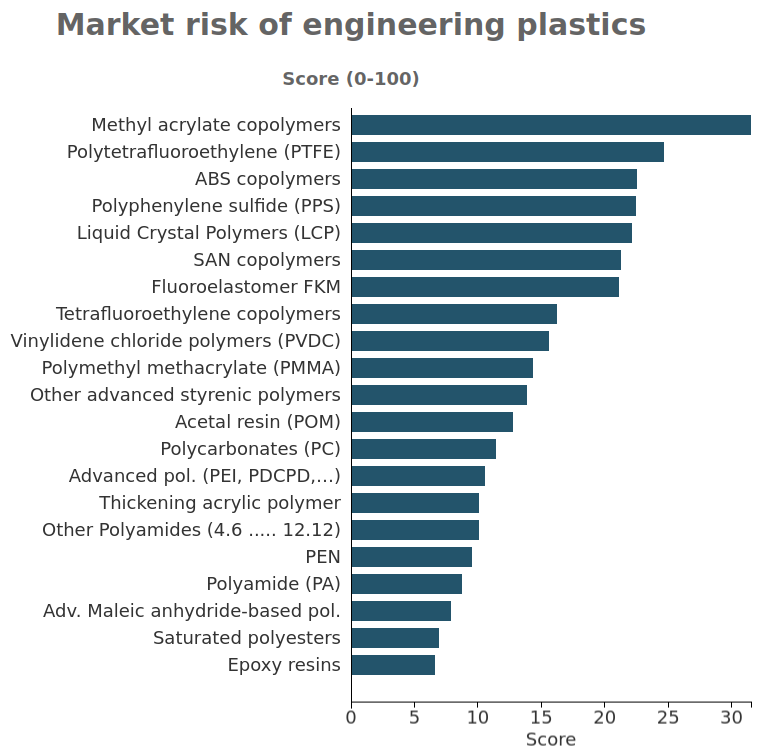
The engineering plastic with the highest market risk is Methyl acrylate copolymers. For this product, the European Union has a significant trade deficit, importing almost all of this engineering plastic from the United States and Canada. The concentration of supply tends to increase market risk, while the stability of trade relations with North America helps reduce this risk.
Following methyl acrylate copolymers, there are six other engineering plastics with significant market risk (score greater than 20). Two of these engineering plastics belong to the group of fluorinated polymers, indicating that China’s growing importance in this sector, combined with its geographic distance, is a risk factor. Two other engineering plastics are derived from styrene (ABS copolymers and SAN copolymers), whose value chain is dominated by China. Finally, two high-performance polymers (namely, Polyphenylene Sulfide (PPS) and Liquid Crystal Polymers (LCP)) also present significant market risk, due to the European Union’s considerable trade deficit for these materials.
For all other engineering plastics, market risk is relatively low.
Conclusions
Until a few years ago, industrialized countries (United States, EU, Japan, and South Korea) held a strong leadership and control over the global market in the important sector of engineering plastics. Over the course of this century, China’s polymer industry has experienced significant growth, initially in base polymers and later in engineering plastics, making China the world’s largest producer. The growth in production has been followed by an increase in exports, positioning China as the world’s leading exporter of fluorinated polymers and placing it on the podium with the United States and Germany in the global market for Polyamides and Saturated polyesters.
The shift in the center of gravity of the engineering plastics industry from the Atlantic to the Asian Pacific coast has increased the logistical risks for European sourcing of engineering plastics. For certain materials where the EU has a high trade deficit, their market risk is considerable.
On average, however, the market risk of engineering plastics is currently modest overall and, in some cases, negligible. Nevertheless , if the shift of the engineering plastics industry towards Asia continues, the number of materials with significant market risk is likely to increase.
[1] For a description of the methodology used by PricePedia to calculate the market risk of a commodity, see: